摘 要:分析醋酸回收装置非均相共沸精馏系统运行现状,在DCS常规控制基础上,应用先进工艺控制(APC)技术,通过克服萃取液蒸发器进料量、进料组分、加热蒸汽压力波动等干扰,稳定主蒸塔组分分布,同时优化主蒸塔中部温度、提馏段灵敏板温度,实现“卡边”优化控制。实测同等稳定负荷情况下,装置蒸汽单耗下降1.8%。
关键词:醋酸回收、非均相共沸精馏、先进工艺控制
1.前言
先进过程控制(Advanced Process Control,APC)是对那些基于模型控制(预测控制)和基于知识控制(智能控制、软测量)等各类计算机控制策略的统称。“先进”是指控制品质优良,但未普遍使用。醋酸浓度较低时,醋酸和水的相对挥发度接近于1,用普通精馏分离较困难,工业上常采用共沸精馏方法[1]。南纤公司醋酸回收工艺采用溶剂萃取和非均相共沸精馏联合法。萃取液组成、流量随上游工序有所波动,主蒸塔进料流量(通过调整蒸发器加热蒸汽流量实现)、塔顶回流、提馏段灵敏板温度等工艺参数也需操作工经常调整。由于操作工调整的及时性和合适性存在差异,对回收醋酸产品质量和能耗产生一定影响。塔顶回流偏大,增加能耗,同时可能导致轻组分进入塔釜,影响塔釜产品质量;回流偏小,醋酸可能从塔顶跑损。2010年,南纤公司成功完成了“醋酸回收装置主蒸塔节能和稳定运行APC项目”。
2.工艺过程分析
南纤公司醋酸回收工艺流程见图1。溶剂与稀酸在逆流萃取塔(1)中接触,萃余相经溶剂回收塔(7)回收溶剂后送废水处理站处理。富含醋酸的萃取液则经蒸发器(2)和残液蒸馏釜(3)去除高沸点的杂质,沸点较低的溶剂、醋酸和少量水在主蒸塔(4)中进行共沸精馏分离。精馏塔顶分出的溶剂和水经冷凝器(5)冷凝后,在分相器(6)中进一步分离,分出的溶剂循环使用,水相则与萃取塔(1)的萃余相一起送溶剂回收塔(7)。精馏塔底得到醋酸产品,该工艺回收的醋酸纯度大于99.5%。
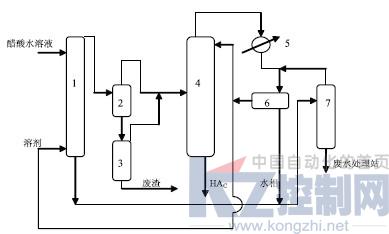
图1 南纤公司醋酸回收工艺流程示意图
1.萃取塔;2.蒸发器;3.残液蒸馏塔;4.主蒸塔;5.冷凝器;6.分相器;7.溶剂回收塔
主蒸塔干扰因素多,变量之间相互影响大。特别是负荷、组分发生波动时,易出现回流不匹配,难以实现最佳运行状态。由于共沸精馏塔存在非线性、大滞后等控制难题,采用简单PID控制策略,无法满足最经济运行要求。在精馏塔中,水、醋酸、多种溶剂形成多元体系。通过模拟,获得每块塔板对应主要组分浓度、温度曲线,见图2。可见,塔上部温度变化比较平缓,该区域汽-液-液三相共存,主要组分为水和共沸剂,醋酸浓度很低。中部是三相与两相的过渡区,温度、浓度、相态的变化均十分剧烈——进料位置以上,共沸剂浓度急剧增大,醋酸浓度迅速减小;进料位置以下,共沸剂浓度迅速降低。底部共沸物浓度极低,共沸剂基本不起作用,温度与浓度的变化规律与醋酸-水二元普通精馏过程相同[2][3]。
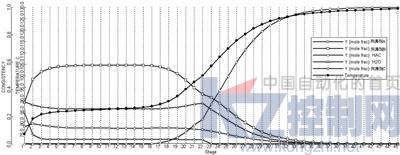
图2 共沸精馏塔关键组分及温度分布图
在共沸精馏过程中,控制共沸剂回流量非常关键。回流量偏多,塔内没有足够水分与共沸剂形成共沸物,溶剂容易落入塔釜,不但增加再沸器负荷,还影响醋酸产品质量;回流量偏少,塔内共沸剂较少,无法将塔内水分及时带出,导致醋酸、水无法有效分离,醋酸从塔顶跑出而损耗。共沸剂分布在塔内无法直接测量,只能依靠塔温度间接指示。共沸剂浓度变化主要集中在塔中部附近,我们利用中顶、中部、提馏段灵敏板、中底温度测点反映共沸剂在塔内分布情况。在生产过程中,回流量偏低时,塔内共沸剂分布逐渐上移,中顶、中部温度升高。如果塔内共沸剂量太少,中顶温度过高,将导致塔顶气相中醋酸含量过大,增加醋酸消耗;由于共沸剂分布上移,提馏段灵敏板温度测点附近共沸剂组分变少,该处温度将有所上升,如果维持灵敏板温度不变,再沸器负荷会下降,而中底部由于以醋酸、水两组分存在的塔板增多,分离精度下降,塔底部的水浓度上升。回流量偏大时,共沸剂分布下移,造成精馏塔中部温度下降,提馏段灵敏板温度测点附近共沸剂组分变多,如果要维持同样的提馏段温度,再沸器负荷将增加,而中底部由于以醋酸、水两组分存在的塔板减少,分离精度增加,塔底部的水浓度下降,但是,如果共沸剂分布下移太多,共沸剂会进入底部,造成回收醋酸不合格。
常规控制策略中,主蒸塔设计了提馏段灵敏板温度与再沸器蒸汽流量的串级控制,其他温度由操作人员根据实际情况调整塔顶回流来控制。从上述工艺分析可以看出,提馏段灵敏温度稳定控制,并不能控制塔内共沸剂分布位置。共沸剂处于不同位置,会影响产品质量以及能耗。操作人员调整回流量,由于精馏塔塔板温度与回流存在大滞后和非线性,难以在时间和数量上精确匹配,易出现较大的波动,无法将塔内共沸剂分布稳定在最佳位置。
3.APC控制策略思路
由于共沸剂分布跟共沸剂在一段塔板的状态相关,单个温度测量值跟共沸剂分布没有直接关系,要综合考虑塔内几个温度状况来判断,而共沸精馏塔内共沸剂变化主要集中在塔中部附近,由此只要估计出中部共沸剂分布状况,即可估计出全塔共沸剂分布。通过物料平衡和模拟分析,结合塔中部不同位置的组分与温度的函数关系,建立正常生产时塔内共沸剂总量变化方程,主要公式如下:
其中,R共沸剂为主蒸塔塔顶回流量;
F共沸剂为进料共沸剂量;
G共沸剂为共沸剂与水形成共沸物后,以气相形式离开塔顶气相量;
k为单位质量水形成共沸物所需的共沸剂量;
M共沸剂为塔共沸剂液相总量;
ml为每块塔板持液量,该参数受气相负荷影响;
X共沸剂(l)表示第l块塔板共沸剂液相含量;
N为共沸精馏塔的塔板数;
y共沸剂(T,P,F)代表共沸剂含量与温度、压力、处理负荷的函数关系。
从上述公式可以看出,要稳定共沸剂在塔内分布,只需将共沸剂浓度突变段的共沸剂浓度稳定即可。共沸精馏塔内的浓度变化可看作是共沸剂代替水的过程,如果需要把共沸剂浓度分布上调或下移,意味要要有适当的共沸剂替换水。在其他条件稳定时,意味着塔内共沸剂总量增加或减少。在实际生产过程中,共沸剂过量,共沸剂液相不断下移,一部分与水形成气相共沸物,汽化到塔顶;一部分替换对应塔板原来的水分,剩余部分继续下降,直到新的平衡。共沸剂回流量与共沸剂塔内分布之间关系具有累积关系,进料中水含量、共沸剂量变化均会影响到共沸剂在塔内的分布。
先进控制采用模型预测控制算法,该算法是利用历史数据和预测模型预测系统未来的输出,并按照设定的性能指标函数滚动优化,计算出一系列的控制作用,对大时滞、强耦合等很多PID 算法不能奏效的被控对象实施有效地控制。模型预测算法采用脉冲响应模型,未来输出值的预测值为:
(5)
为了克服扰动和模型失配引起的偏差,采用当前实际值与模型计算值比较,用其偏差修正预测值:
(6)
设定优化控制的目标函数为
(7)
通过在约束范围内优化上述目标函数计算得出系统将来的控制作用[4]。
其中,ym为输出变量模型预测值;
h为是输入输出模型响应序列;
u为输入序列;
yp、yk分别为校正后预测值和实际值;
βj为校正系数;
ysp为输出变量期望目标值;
Q、R均为权矩阵;
HP为优化时域;
HC为控制时域。
4.应用方案及其实现
主蒸塔APC项目以保证产品质量和降低蒸汽消耗为目标,在DCS常规控制的基础上,应用先进控制软件建立整个主蒸塔的模型预测控制器,通过克服萃取液蒸发器进料量、进料组分、加热蒸汽压力波动等干扰,稳定主蒸塔组分分布,同时优化主蒸塔中部温度、提馏段灵敏板温度,实现“卡边”优化控制,实现精馏塔最低能耗运行。我们提出的功能要求包括:
(1)设备运行安全性
考虑塔顶循环冷却水阀位,以及塔釜加热量变化,避免冷却、加热负荷不合适,而导致塔压偏高或加热蒸汽流量过大引起的设备运行不正常问题。解决原先塔顶压力控制,和提馏段灵敏板温度控制互不相关的问题。
(2)主蒸塔系统的萃取液处理负荷,和萃取液进料储槽之间的物料平衡
根据萃取塔负荷以及萃取液进料储槽液位变化趋势,自动平稳调节储槽出料流量。在容许储槽液位于一定区域内平缓变化的前提下,尽量保持进汽液分离器物料流量稳定性;根据汽液分离器进料流量和萃取液储槽液位变化情况,优化调整蒸发器加热量,以保持装置物料进出平衡。
(3)主蒸塔产品质量控制
根据共沸精馏塔组分分布特点,特别关注共沸剂组分变化敏感区域,结合以往生产过程数据及检测值(主蒸塔塔底回收醋酸检测值、塔顶馏出物水相醋酸含量滴定值),得出产品质量与精馏塔过程数据的影响关系,预测实际生产过程中产品质量随工况变化趋势,以自动调整主蒸塔塔顶回流流量和提馏段灵敏板温度,保证塔釜、塔顶的质量指标要求。通过综合考虑塔顶部、中顶、中部温度,保证塔顶产品质量。其中,中顶、中部温度是关键温度,因为这两个温度是共沸剂组分变化敏感区域。塔釜产品(回收醋酸)质量,主要关注提馏段灵敏板温度,中底和底部温度差值,这个温差较好反映塔釜产品质量组分变化。
(4)能耗最小化优化
根据产品质量预测值、实际化验值及生产过程数据,在保证质量指标条件下,不断的优化回流量及关键受控变量目标值;同时根据塔顶冷却负荷状况,逐渐调整塔顶压力,提高分离能力,实现精馏塔能耗最小化。整个优化过程逐步推进,生产工况平缓渐变,不给装置带来额外波动。
以上功能通过多变量预测控制器来实现,并根据精馏工艺生产要求,建立了各工艺参数、操纵变量的优先级控制,充分考虑精馏塔产品质量和能耗的协调控制,维持精馏塔处于最优运行状态。主蒸塔多变量控制器变量主要包括操纵变量、干扰变量和被控变量,见表1。
表1 主蒸塔节能和稳定运行控制器变量列表
5.应用效果
主蒸塔节能和稳定运行APC系统投用后,萃取液蒸发、精馏操作稳定性提高,见图3、4。正常情况下,基本不需要人工手动干预就能够保持生产平稳运行,减少了操作人员劳动强度,实测同等稳定负荷情况下蒸汽单耗(萃取液蒸发器+主蒸塔再沸器+残渣蒸馏釜)下降1.8%。
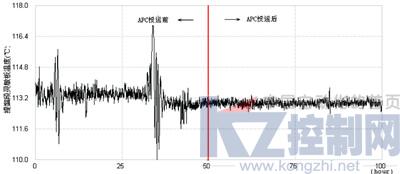
图3 主蒸塔提馏段灵敏板温度控制效果对比
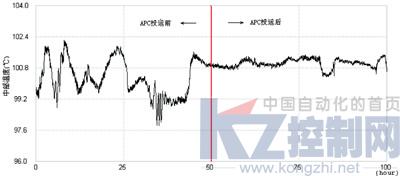
图4主蒸塔中部温度控制效果对比
6.结束语
醋酸回收装置以多设备交叉联接,存在热集成、物料集成。我们首次使用APC技术,存在一些问题。萃取液精馏系统与上游工序关联密切,当上游设备出现故障或物料不平衡等(例如醋片生产短期停车,导致萃取塔负荷变化增大),在一定程度上影响APC的投用效果,此时需操作人员进行人工干预,尽可能保持装置平稳运行;萃取液蒸发器切换期间,主蒸塔运行波动大,先进控制效果不理想。今后,我们拟考虑稀酸萃取的影响,关联萃取关键工艺参数(溶剂/稀酸),从更大的系统上考虑问题,进一步稳定主蒸塔进料组分,提高APC实施效果。
参考文献
[1] 李新利,唐聪明,萃取精馏分离醋酸-水溶液溶剂研究进展及机理分析,天然气化工,2005,30(6),6366
[2] 王丽军、李希、张宏建,乙酸-水-乙酸正丁酯三相体系的热力学分析与共沸精馏过程模拟,化工学报,2005,56(7):1260~1266.
[3] 时在国,PTA 装置共沸精馏塔脱水系统,聚酯工业,2005,18(5): 33~36.
[4] 邵惠鹤,工业过程高级控制,上海交通大学出版社,1997: 258~260.
摘自《自动化博览》2011年第十期
|