(中油龙慧自动化工程有限公司,北京 100101)黄懿雪,李国栋,郭长滨

黄懿雪(1971-)男,福建人,高级工程师,现就职于中油龙慧自动化工程有限公司,研究方向为长输管道自动化系统。
摘要:本文针对成品油混输监测系统的功能和精度要求,提出了管段流量界面法和逐站密度检测修正方法结合来进行成品油批次计算;在介绍成品油管道现场仪表数值特点的基础上,论述了成品油混输监测系统研究过程中批次里程计算、逐站密度修正算法、流量数据特点、当量管道长度计算和修正方法,该方法已经在兰成渝、西部成品油管道上进行实际应用。
关键词:混合输送,混油界面,当量管道长度,批次跟踪
Abstract: In order to satisfy the functional and precision requirements of mixed product oil transfer supervision system, this paper proposed a combined solution to calculate the batches of product oil by integratethe method of pipeline flow interface and the method of per-station density correction together. Based on the introduction of on-site meter value features of product oil pipeline, this paper discussed the calculation of batch mileage, the algorithm of per-station density correction, features of flow data and the calculation and correction of equivalent length of pipeline in the R &D process of the mixed product oil transfer supervision system. At present, this solution has been used on Lanzhou-Chengdu-Chongqing Product Oil Pipeline and the Western Product Oil Pipeline.
Key words: Mixed product oil transfer; mixed oil interface; equivalent length of pipeline; batch tracking
1 前言
为了提高管道输送效率,成品油管道普遍采用了顺序输送方式连续输送多种类型油品,管道沿途设有多个分输站,对输送的油品进行分输。随着油品分输,管道流量呈阶梯状递减,管径也随之发生变化。
不同的油品在密闭管道中顺序输送,由于不同油品的相互扩散会产生混油现象,所以在接合面处出现了一段密度介于相邻两种油品密度之间的混油区。随着输送距离增加,混油区体积也不断增加。在实际生产中,管道输送一般采用首站场不同油品连续注入、中间站场纯油注入或分输、管道末站统一处理混油区油品的工艺流程。为了保证中间站场尽可能多的纯油注入或者分输,末站场尽可能少的混油处理,都需要调度人员和工艺人员实时准确的监测到管道中各种油品的里程和混油区体积。
成品油混输监测系统主要是从管道SCADA系统、管道数据平台获取管道运行过程中的工艺数据,自动跟踪并计算管道混输的批次数量变化、批次里程变化、批次混油变化,从而为管道调度人员和工艺人员提供油品注入、分输和混油切割处理操作的依据。通过混输监测系统,调度人员和工艺人员可以准确监测管道中多个混油区的位置和长度,可以尽可能的多分输油品,减少末端统一处理的混油体积,保证销售油品的品质,提高管道输送的经济效益。
图1 混输监测系统数据层次示意图
调度人员需要随时监测管道输送油品批次和批次位置,这是对成品油进行分输的主要依据,另外,管道停输、末站混油处理等工艺操作也需要准确的批次数据。混油监测系统是管道调度人员进行批次跟踪作业的重要依据,因此,它的计算精度高低直接影响调控成品油管道的运行管理水平。
本研究根据成品油管道混输监测的需要,对混输监测技术进行了研究,并根据研究成果实现了混输监测软件的开发,目前该软件已应用于西部成品油、兰成渝管道。
2 批次里程计算方法
批次里程计算是混输监测系统基本的计算,一般以管道流量仪表传送上来的管道现场流量数据为主要参数。流量仪表的测量值进入流量计算机,流量计算机根据设定的计量标准,如AGA、ISO、国标标准进行换算后输出。目前,混输监测系统常用的批次里程计算方法一般采用管道流量累积法,即基于批次油品在当前管道内油品体积来进行批次里程计算,管道流量累积方法的原理大致如下:
如图2所示,顺序输送的管道中存在三个批次的油品,90#汽油用红色表示,93#汽油用绿色表示,0#柴油用黑色表示。
图2 管道分输、注入和批次示意图
管道具有若干个分输、注入分支。
由于油品的可压缩性近乎为零,并且管道运行于满流状态下,某一个时刻或者一个时间段内,分输和注入的油品流量相等,用公式表达如下:
式中:Qi 为管道输入的流量, Q0为管道输出的流量。
在某一个时刻,管道内管道总管存等于各个顺序输送批次的体积和,公式表达如下:
式中: Vb为批次体积,Vp 为管道总管存。
在某一个时刻,某个批次体积为:
本项目针对管道流量累积法的原理、过程和准确度进行研究后,提出了一种基于分段计算的管段流量界面法的里程计算方法。管道内按照不同管段的流量,各个批次单独进行界面计算,某个批次界面位置根据批次当前的流量确定。公式:

L为混油段中间位置界面距离上一个站的里程,m3;Qa(t) 为批次界面的瞬时速度。
一个批次的油品,由于有分输和注入等因素,在管道中的流速是不同的。在管道输送过程中,油品的分输和注入都是在站场完成的,因此,在两个站场间的干线流量是相同的,都等于前一个站场的出站流速。
从混油里程的流量累积法和管段流量界面法的原理和过程可以知道,采用流量累积方法计算批次混油体积涉及到的管道流量数据很多,任何数据误差,都会导致计算误差;而管段流量界面方法,仅仅和混油界面所在管段的流量有关系,因素单一,计算精度高。而且,界管段流量界面方法的一个最大优点在于可以分段迭代计算和密度修正。
3 密度检测修正算法
采用管段流量界面法进行批次里程计算的时候,随着油品的管道的运行里程增加,累积的计算误差越来越大。在经过大分输量站场时,由于相邻两个管段的干线流量差别较大,会使计算误差达到失去计算意义的程度,因此,管段流量界面法需要结合干线密度检测修正来进行计算修正。
在成品油管道的各个站场,都安装了密度检测仪表,通过仪表密度的变化,来监测管道上批次的到站情况。密度判断要求不能误判,既不能将密度的波动认为界面到站,也不能界面到站算法没有判断出来。
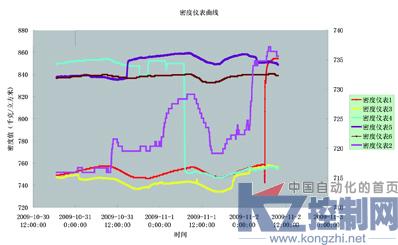
图3 兰成渝管道站场线密度仪表数据变化趋势曲线
图3为兰成渝管道在三天内的密度变化曲线,是若干批次油品在顺序流经管道过程中,干线流量计的计量数据。从图中可以看出,随着白天温度上升,油品密度降低;夜晚温度降低,油品密度升高。同一批次油品由于不同的生产工艺,密度值也会有所变化。另外,不同密度仪表在这个过程中也会具有不同特点的波动。从图中的六条密度变化曲线可以看到,密度的变化符合上述因素,其中,密度仪表4在2009年11月1日7点05分从密度845.973变化到2009年11月1日7点42分密度751.788,表明管道内顺序输送的柴油批次到汽油批次的变化。密度仪表1在2009年11月2日5点49分到6点15分密度从757.664变化到853.773,表明管道顺序输送的汽油批次到柴油批次的变化。
为了消除管段间批次里程计算误差累积产生的管道批次里程计算误差,系统需要实际的批次油品到站时刻,并以在此时刻为起点,重新开始下一管段的批次里程计算。批次油品到站的时刻,在混油监测系统中是通过干线密度仪表变化扑捉到的。由于现场密度变化的复杂,准确及时扑捉油品到站产生的密度变化需要根据实际工艺数据的长期分析、研究来实现。混输监测系统的油品到站产生的密度变化扑捉算法大致过程如下:
(1)限制条件:为了降低错误扑捉的情况发生,仅在系统计算的混油界面位置在站前后10公里范围内启动对该站密度计的检测算法。
(2)过滤:为排除异常的密度数值,通过密度值范围和密度值变化率方法剔除变化异常的密度数值(如上图曲线中的短时间内变小很多的值和小于700大于900的所有值)。
(3)投票算法:通过密度计的多个历史值进行投票算法,并结合变化率检测密度是否是在上升或下降。
(4)判断:如果判断出密度的上升或者下降,刚好和站附近界面的油品特征对应时,确认是一次界面到站,对界面进行校正。如果在检测范围内一直没有检测到密度变化,认为密度计没有开启或者故障了,不进行修正。
4 当量管段长度计算和修正方法
混输监测系统的计算依据实际的管道工艺数据,这些工艺数据包括静态数据和动态数据。静态数据在混输监测系统初始化后一般不发生变化,典型数据包括管段长度、管段公称外径、管段壁厚、管段地温等管道设计参数。静态数据存储于混输监测系统的模型配置文件中,用户根据监测管道的设计数据来完成模型文件的配置,混输监测系统启动后读取指定的模型文件来完成系统计算过程的初始化。动态数据在混输监测系统的每一个计算过程中都可能发生变化,典型数据包括管段油品温度、管段流量数值、管段压力。动态数据来源于管道SCADA系统或基于SCADA系统的中间实时数据库平台,混输监测系统的每一次计算,都需要获取这些参数的实时数值。在混输监测系统的周期计算过程中,配置的管道静态数据和获取的动态实时数据都具有一定的误差。管段公称外径由于热胀冷缩现象会随着管段地温发生周期变化。温度、流量、压力数据来源于现场测量仪表,测量仪表的测量误差主要由仪表的系统误差和偶然误差引起的,根据仪表的精度的分析,偶然误差较小,且方向不同,累积效果不明显。系统误差因素引起的变化缓慢但时间累积效果明显,对计算的影响不容忽视。导致管段公称外径变化及油品体积变化的管段地温一般随着管段当地的季节因素周期变化。所有这些误差都会引起混输监测系统在不同管段内的批次里程计算精度产生长期缓慢的变化,而且变化原因复杂、变化趋势不易分析和排除。
为了避免混输监测系统由于管道模型配置、运行工艺参数以及其它因素产生的计算误差,提高混输监测系统批次里程计算的精确度,提出了当量管道长度的计算方法。用考虑了各种因素综合作用的当量管段长度来替代配置的管段长度来进行批次里程计算。当量管道长度等于各个管道构成管段的当量管段长度总和。当量管段长度在数值为油品在上一站出站到下一站密度仪表检测到油品进站时间内,混输监测系统以包含各种误差因素条件下的管道工艺参数计算出来的油品运行里程。批次里程计算的各种输出值,包括批次界面里程、批次界面出站里程、批次界面距离下站里程、批次界面到站时间等都是以当量管段长度作为管道实际长度来计算出来的。
当量管道长度的方法本质上就是以前期计量的结果倒推输入参数,并以倒推的输入参数来计算本期的计算结果。
对于不同管道、不同管段,当量管段长度不同,并且不断变化的,因此,管段的当量管段长度数值在每一个批次到站都会重新计算。为了避免意外情况发生后产生的错误数据,混输监测系统对当量管段长度数值的更新采用更新算法进行控制。一般采取比较简便的判断算法即可:当系统批次里程计算误差连续三次超过系统精度要求(管道全程不大于3公里),且三次之间的误差在2公里以内,系统自动根据计算结果更新管段的当量管段长度。
当量管道长度的算法有效解决了季节、温度、仪表系统误差等长期缓慢变化因素对界面里程计算的影响,减少了系统校准的次数,提高了系统长期运行的精度。
5 流量数据修正算法
混输监测系统在西部成品油、兰成渝管道运行过程中,管道运行工艺参数来源于管道上安装的各种测量仪表,数据上行过程由于现场测试仪表、中心SCADA系统、中心的中间数据库平台,仪表故障、维护以及传输、SCADA系统切换等原因,系统从中间数据库获取的数据存在异常情况。
对于混输监测系统来说,由于数据获取的环节多,中间经过多次存储和转换,异常数据的产生是不可完全避免的。为了排除异常数据引起的大误差,需要对系统获取的管道流量数据进行校验和修正。通过对管道实际生产过程中的大量数据进行统计并结合管道流体理论分析,发现可以用管道流量数据环公式来进行流量仪表数据值的修正。管道流量数据环公式的过程在于:①管道流量仪表数据包括干线仪表数据和分支仪表数据,分支仪表数据包括分输、注入;②沿着管道流体运动方向建立流量环,每个环包括两个干线仪表数据和多个分支仪表数据;③每个环一般包括输入-分输-输出三个流量值;④相邻两个环通过同一流量值关联,即上一个环的输出,是下一个环的输入。对于没有分支的环节,可以认为其分输为零即可;⑤环质量确定,根据输入减去分输与输出偏差5%的原则,确定环的质量为正确和错误。在一个流量环中,按照公式来确定环的质量。环的质量分为优环和劣环。⑥从起点开始遍历环中流量数值,在管道模型中寻找连续正确环,按照流量值最多原则确定修正起点;⑦从起点开始,向两个方向按照公式进行计算,修改劣环的数据。
6 混输监测系统在兰成渝、西部成品油管道上应用
西部成品油管道起点乌鲁木齐,途经天山、戈壁滩、祁连山区、黄土高原等地区,终点为兰州,全长1858km。跨越多少个省区,管道设计输量为乌鲁木齐~新堡中间站管径为Φ559,新堡中间站~兰州末站管径为Φ508。包括18个站场,24个阀室,5个高点。其中分输站场5个,分输阀室4个。
兰成渝成品油管道起始于甘肃省兰州市兰州炼油厂附近,经四川省成都市到达重庆市。道全长1247km,设计年均输量为(最大可达 ),输送油品主要为#90汽油、#93汽油和#0柴油(随市场需求情况还可以输送航煤、LPG和其它石油产品)。包括15个站场,15个阀室,3个高点,其中分输站13个,分输阀室3个。
混输监测系统现场运行需要一定的调试和学习过程,在西部成品油管道和兰成渝管道的工程实施中,系统大概经过10个批次的调试和学习后,基本达到了全线不大于3公里的计算精度。期间,系统在管道停输、启输以及中心数据库切换的情况下基本保持运行可靠、计算准确。
7 总结
通过在混输监测系统中以管段流量界面法作为批次里程计算的主要方法,并以流量数据修正方法、当量管道长度计算和修正方法等方法作为辅助,有效解决了混输监测系统的计算精度问题。
摘自《自动化博览》2010年第七期
|