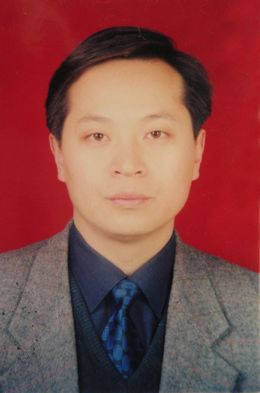
作者简介:
苏宏业(1969-),男,博士,教授/博导,中共党员。1995年6月毕业于浙江大学工业自动化专业,获工学博士学位; 2000年12月被聘为浙江大学教授;2001年12月被聘为浙江大学博士生导师;1999年10月起至今任浙江大学智能系统与控制研究所(原名先进控制研究所)副所长。
主要研究复杂工业过程建模、控制与优化的理论、技术及实现。先后作为项目负责人承担国家杰出青年科学基金、国家科技攻关项目、国家教育部高等学校优秀青年教师教学和科研奖励基金、国家高技术研究发展计划(863计划)重点项目等国家和省部委纵向课题十余项。与他人合作出版专著三部,在国内外学术刊物发表论文100余篇,其中SCI收录60余篇,SCI他引50余次。申请国家发明专利16项,已授权8项。研制开发了先进控制与优化工程化系列软件与实施技术,并大力进行应用推广,目前该系列软件及技术已应用60余套,广泛应用于流程工业重大与关键复杂生产装置与企业,取得显著的经济效益和社会效益,较好地实现了科研成果向生产力的转化。
摘要:本论文提出了炼化企业瓦斯平衡与优化调度的整体解决方案,其核心思想为基于瓦斯产需预测模型和瓦斯系统优化调度模型,实现瓦斯系统的“事前调度”和“定量调度”。实践证明,该解决方案可以明显提高炼化企业瓦斯系统的调度和管理水平,并通过减少瓦斯排放和节约补烃量,取得了明显的节能减排效果。
关键词:瓦斯系统 产需预测 优化调度 节能减排
1 引言
瓦斯,俗称炼厂气、燃料气、不凝气、干气等,是石化企业最重要的二次能源之一,来自于石化企业的各类一次和二次加工装置,同时也是各加工装置加热炉和锅炉的最主要燃料来源。由产瓦斯装置、输送瓦斯单元(包括低压瓦斯管网、高压瓦斯管网、瓦斯压缩机)、气柜和火炬系统、耗瓦斯装置等组成的系统,称之为瓦斯系统。
瓦斯系统是石化企业能源浪费和环境污染较为严重的环节。目前,国内大部分石化企业的瓦斯系统普遍存在如下几个问题:
(1)瓦斯产耗检测手段不够完善,也没有统一的公用工程(包括瓦斯系统)实时监控平台,无法从源头上控制乱排乱放现象的发生;
(2)调度人员凭经验对瓦斯系统进行调度,无法准确预估全厂瓦斯产需平衡的变化规律和趋势,当瓦斯产大于耗、气柜超限时,需要通过燃放火炬来平衡,当瓦斯产小于耗、高压瓦斯管网压力不足时,需要补充重整碳五、液化气等轻烃资源,不可避免地造成了环境污染和大量资源的浪费;
(3)调度人员凭经验对瓦斯系统进行调度,经常需要通过生产装置改变操作工况来稳定瓦斯系统,造成操作成本增加和安全隐患。
针对国内石化企业瓦斯系统的具体特点,研究瓦斯产需预测、瓦斯管网模拟、瓦斯系统优化调度等关键技术,建设瓦斯系统实时监控和优化调度平台,将基于经验的调度提升到基于模型的“事前调度”和“定量调度”,可以明显提高瓦斯系统的操作安全性和经济性,减少瓦斯放火炬时间,减少瓦斯系统补烃量,为企业带来明显的经济效益和社会效益。
2 瓦斯平衡与优化调度模型的建立
为从根本上解决对瓦斯系统产需变化无法准确把握、完全凭经验进行调度的现状,必须对瓦斯产需情况进行准确预测。瓦斯产需预测的主要内容是,对炼化企业各生产装置未来一段时间内的瓦斯产需变化进行建模与预测,提供未来各装置瓦斯产需的准确预测信息,从而实现基于模型的调度。
在瓦斯系统产需预测模型中,借鉴了软测量的思想,即用与瓦斯生成量或需求量紧密相关的辅助变量来预测瓦斯生成量或需求量。所不同的是,在瓦斯系统产需预测模型中,是用当前时刻和过去一段时间的辅助变量数据来预测各生产装置在未来一段时间内的瓦斯生成量或需求量。同时,在瓦斯系统产需预测模型中,也借鉴了时间序列建模的思想,即用当前时刻和过去一段时间内的瓦斯生成量或消耗量数据来预测未来一段时间内的瓦斯生成量或需求量。因此,瓦斯系统产需预测模型综合了软测量和时间序列建模思想。
在实现瓦斯产耗预测的基础上,可以建立瓦斯系统优化调度模型,其核心思想是以未来一段时间内的瓦斯系统总的操作成本最小为目标,通过优化压缩机操作负荷、优化液化气、轻烃等贵重资源的气化策略、优化燃料油的补充策略,减少瓦斯放火炬时间,减少补烃量,实现节能减排目标。
瓦斯系统优化调度模型由目标函数、约束条件和操作变量构成。瓦斯系统优化调度模型的目标函数为:
.jpg)
瓦斯系统优化调度模型的约束条件包括物料平衡约束、能量平衡约束、能量需求约束、操作约束和装置约束等。
物料平衡约束:

能量平衡约束:

能量需求约束:

操作约束:


装置(气柜)约束:
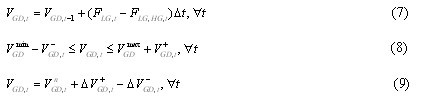
装置(高压瓦斯管网)约束:


装置(加热炉锅炉)约束:

在式(1)~(13)中,瓦斯产量 需求量 正是瓦斯系统产需预测模型的输出结果。因此,所建立的瓦斯系统优化调度模型是基于预测数据的。
由目标函数式(1)和约束条件式(2)~(13)构成瓦斯系统优化调度模型,该模型由于存在0-1变量,需要采用混合整数线性规划方法进行求解。
3 瓦斯平衡与优化调度系统整体架构
浙江中控软件技术有限公司经过多年的科研攻关和现场实践,首次提出了由“2”个集成平台、“4”套系统架构的石化企业瓦斯系统平衡与优化调度整体解决方案,如图1所示。
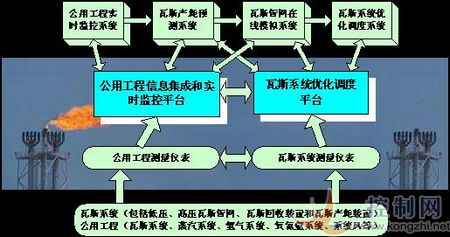
图1 石化企业瓦斯系统平衡与优化调度整体解决方案架构图
该解决方案具有如下特点:
(1)建设 “2”个集成平台——公用工程信息集成和实时监控平台,瓦斯系统优化调度平台;
(2)公用工程信息集成和实时监控平台实现企业主要公用工程介质的实时监控、故障诊断和综合管理,从源头控制乱排乱放现象,提高公用工程的操作安全和平稳性;
(3)瓦斯系统优化调度平台,基于瓦斯产耗预测和瓦斯管网模拟模型,以调度周期内燃料消耗成本最低和操作最平稳为目标,建立优化调度模型,给出未来调度周期内的优化调度建议,实现基于模型的“定量调度”和“事前调度”,通过减少瓦斯排放,优化燃料配置,节约轻烃资源,取得节能减排效果。
(4)该解决方案具有在炼油、石化、化工、钢铁企业广泛的适用性、开放性和可移植性,可以为企业带来明显的经济效益和社会效益。
4 应用效果
瓦斯平衡与优化调度整体解决方案在中国特大型炼化企业镇海炼化得到了成功应用,取得了如下应用效果:
(1)基于公用工程信息集成和实时监控平台,实现了企业整个公用工程(包括瓦斯、蒸汽、氢气、氮气等子系统)的实时监控和综合管理,成为调度人员的日常必备工具,有效避免了乱排乱放现象的发生;
(2)基于瓦斯产耗预测系统,可以准确预测未来一段时间内(如24小时内)瓦斯产耗平衡的变化量和变化趋势,主要装置瓦斯预测模型的平均预测误差绝大多数在3~10%之间,提高了调度的预判性,为调度人员实现“事前调度”提供了有力支撑;
(3)基于瓦斯管网在线模拟系统,准确获得了低压和高压瓦斯管网内部每个节点和每个管段的详细信息(包括温度、压力、流量、组成、热值、压降和流向等),主要节点热值预测误差约为4%~7%,为调度人员实现精确调度和“定量调度”提供了有力支撑,提高了瓦斯系统的安全性和操作平稳性;
(4)基于瓦斯产耗预测和瓦斯管网在线模拟模型,建立了优化调度模型和专家系统,优化调度模型给出的调度方案与现场的匹配度大于90%,实现了有效的瓦斯系统优化调度,降低了瓦斯系统补烃量,减少了瓦斯排放,瓦斯基本不放火炬,取得显著的节能减排效果。
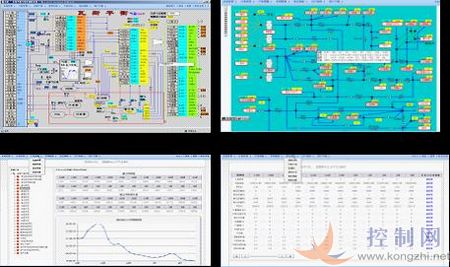
图2 瓦斯平衡与优化调度系统界面示意图
通过对比瓦斯平衡与优化调度系统在镇海炼化投运前后一年的统计数据,其经济效益核算如下:
(1) 低压瓦斯排放时间从投运前的207小时减少到投运后的15小时,同比减少192小时(即减少92.8%),累计减少低压瓦斯排放230吨;
(2) 瓦斯系统补烃量从投运前的14045吨减少到7996吨,同比减少6049吨(即减少43.1%)。
5 结束语
瓦斯平衡与优化调度系统填补了国内石化企业瓦斯系统平衡与优化调度信息化平台技术的空白,属于国内首创,其成功应用于镇海炼化,为企业带来明显经济效益,获得用户高度评价。
|