0 引言 随着智能仪表和现场总线技术越来越多的应用于工业现场,大量现场信息通过智能仪表直接进入监控计算机或通过现场总线传至计算机后,存在计算机内部应用程序与现场信息的共享与交互问题[2]。另一方面,现场控制级作为企业整个信息系统的底层部分,必然需要与工程师站、专家站进行信息共享。由于控制系统往往由不同的厂商开发,相互兼容性差,各级控制系统间难以有效地进行信息交互。 碳素阳极是铝电解工艺中至关重要的原料。某厂现有碳素阳极生产线采用A-B公司的可编程控制器(SLC系列),借助RSLinx通讯软件、RSView32组态软件实现了焙烧过程监控。但目前该生产线自动化水平较低。操作工需要时刻监视生产过程,人工定时记录大量的温度、压力等参数,并根据历史数据来修改设定参数。原有工程师站及专家站由不同的厂商开发,与现场级操作站可交换的信息很少。 鉴此,本文提出了一种基于OPC技术的多级控制网络结构,可实现现场控制级、工程师站、专家站的信息共享,并通过OPC将现场控制系统与Access数据库、VB等应用软件连接起来,将专家知识库、过程建模与仿真同现场生产无缝的连接起来,组成一种开放的、即插即用的工业实时监控系统(ONPS)[1]。 1 OPC概述 OPC(OLE for Process Control)规范是由AB、西门子等200多家世界高水平的自动化厂商与微软合作制定的一项工业标准。这个标准定义了在微软操作系统下的不同客户程序之间交换实时自动化数据的方法。 1.1 OPC技术规范 OPC 技术以组件对象模型和分布式组件对象模型(COM/DCOM)技术为基础,采用客户/服务器(Client/Server)模式,定义了一组COM对象及其接口规范。 OPC对象主要包括服务器(Server)、组(Group)、和项(Item)。OPC 服务器对象除了维护自身信息外,还作为组对象的容器,可动态地创建或释放组对象;而组对象相对于项而言也是一个包容器,它提供了一套管理项的机制;OPC 项则表示了与OPC 服务器中数据的连接,包括值(Value) 、品质(Quality) 、时间戳(Time stamp) 三个基本属性[3]。 OPC提供了两个应用程序的接口,一个是定制接口(Custom Interface),供C/C++开发的应用程序使用,一个是自动化接口(Automation Interface),供VB和VBA用户使用。许多应用程序如Matlab、Access等都可使用自动化接口快捷的与OPC服务器建立联系。见图1

图1 两种OPC接口
1.2 使用OPC的优点 OPC规范出现之前,自动化设备厂商在生产硬件的同时,必须提供硬件相关的驱动程序。软件开发商只有得到硬件驱动程序后,才能开发访问该硬件的上层程序。一旦硬件设备升级,软件开发商必须重新针对驱动程序做相应的修改,增加了系统维护的成本。系统集成商急需一种开放的、即插即用的驱动程序。 另外一方面,由于工业过程控制对象的复杂性及信息参数较多,传统工业过程系统采用两级或单级控制结构。工业过程数据只能停留于现场操作站。随着Intertnet/Intranet远程控制的出现,以及复杂控制算法越来越多的应用于复杂工业过程控制,大量控制系统分为现场操作级/工程师站/专家站三级控制结构。不同控制级之间需要进行无缝的数据连接。 OPC技术建立了一组符合工业控制标准的接口规范,将现场信号按照统一的标准与SCADA和HMI等软件无缝连接起来,同时将软件和硬件分离开来,为硬件制造商和软件开发商划分了界限,使软件层不再依赖具体的设备硬件层,大大提高了控制系统的互操作性和适应性。见图2

(a) 传统数据访问方式 (b)OPC下数据访问方式
图2 两种数据访问方式的对比
1.3 OPC发展前景 OPC基金会自成立至今,会员已经超过220家,世界上各主要的自动化仪表生产商,自动化系统开发商都是该组织的成员。经过OPC基金会几年高效的工作,目前已经推出了OPC数据访问(Data Access)、报警与事件(Alarm and Event)规范和历史数据访问(Historical Data Access)规范。目前得到广泛应用的是OPC数据访问规范,它主要解决服务器端和客户端的实时数据存取问题[4]。 OPC技术作为一项成熟的工业标准,近年来引起广泛关注,许多高校与自动化厂商都致力于OPC产品的研发。一些国际著名的控制类公司,如AB,西门子,ABB等都针对其硬件产品和组态软件开发了OPC产品,用户无需使用C++/VB进行繁琐的编程工作,就可以利用OPC开发控制系统。在本文中,使用了AB公司的组态软件RSView32,该软件支持OPC技术,具体的使用方法参见3.1。 在应用研究方面,许多科研人员利用OPC所带来的巨大便利,开发了许多优秀的工业控制系统。在文献3中,作者开发了一种基于OPC技术的先进控制算法平台,该平台可以加载和仿真各种先进控制算法,并通过OPC技术和第三方DCS系统进行数据交换,实现了对复杂工业系统的先进控制。在文献1中Jun Liu,Khiang Wee Lim等人提出了一种基于OPC技术的开放的(Open)、公共的(Nonproprietary)、即插即用的(Plug-And-Play)工业实时监控系统(ONPS)。该系统为独立分散的过程监控与工控软件提供了一种标准的数据共享的方法,同时将仿真与实际应用无缝的连接起来。
2 系统结构 2.1 生产系统简介 碳素阳极生产线由五部分组成:原料系统、循环水系统、燃烧机系统、余热炉系统和煅烧系统。见图3
 图3 碳素阳极生产线组成图
原料系统:将焙烧原料生石焦破碎、电磁分离,通过电动斗提和传输皮带将原料送至煅前仓供煅烧系统使用。操作工根据料仓高度就地或远程控制各个电机的启停。 燃烧机系统:为煅烧大窑提供天然气和空气,操作工根据炉内温度调节燃气阀与空气阀开度大小。在自动控制状态下,可在工程师站或专家站改变空气与燃气的配比。 煅烧系统:煅烧系统主要由煅烧大窑和冷却窑组成。生石焦经过煅烧大窑煅烧后,送至冷却窑冷却。煅烧窑内温度及冷却窑的温度都是影响产品质量的重要因素。开环监控状态下操作工通过改变二次风机与三次风机的转速来改变煅烧窑温度,通过改变冷却窑内喷水的流量来改变冷却窑出料的温度和湿度。同时为了使气体充分燃烧,还需要检测大窑尾气的含氧量。在手动控制状态下,操作工根据含氧量的大小设定燃烧室配风调节阀的开度。 余热炉系统:煅烧窑产生大量的高温气体,余热炉系统可回收利用这些气体,供工厂生活取暖。同时该系统配备了水磨除尘装置,可净化排放的气体。与煅烧系统一样,余热炉系统有大量的参数需要监控。如锅炉蒸汽温度、压力;锅炉给水流量、给水压力;除尘器压力、温度等等。 循环水系统:为煅烧系统提供冷却水,向余热炉系统提供锅炉用水。
2.2 计算机网络控制结构 碳素阳极生产现场有5台A-B可编程控制器(SLC504),分别控制原料系统、燃烧机系统、煅烧系统、余热炉系统和循环水系统。考虑到生产过程比较复杂,产品质量受多种因素影响,系统采用多级控制网络结构。见图4
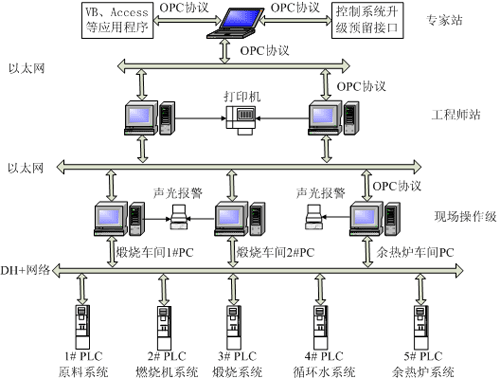
图4 碳素阳极生产多级控制结构图
现场操作站有三台研华工控计算机。每台计算机上都装有A-B公司的组态软件RSView32,借助RSLinx通讯软件和DH+网络与PLC进行数据交换。煅烧车间的两台工控机为主热备份,主要负责监控原料系统、燃烧机系统、煅烧系统和循环水系统。现场操作级主要有以下功能: (1).监控原料系统料仓高度,根据该高度就地或远程控制给料机、破碎机、皮带传输等电机的启动停止。 (2).监控煅烧系统、循环水系统、余热炉系统各个检测点的温度、压力、流量,在系统手动状态下调节各个执行机构的输出量。 (3).设定系统设备连锁运行,故障处理时设备的启停。 (4).作为OPC服务器向工程师站和专家站传递现场所有参数,并接受上一级发送的控制参数。 工程师站有两台研华工控计算机,装有RSView32组态软件和RSLogix500 PLC编程软件。工程师站主要有以下功能: (1).集中显示生产过程所有可视化信息,包括各检测点数值、各个电机运行状态、控制模式、给定数值等。 (2).对整个生产过程进行初始化设置,并可在线修改各个控制回路控制器参数。 (3).可改变整个系统各个控制回路手动、自动控制模式。 (4).生成生产过程各种数据的班报、日报、月报、年报。 工程师站利用RSView32自带的OPC功能与现场操作站进行数据交换,减少了DH+网络的通信负担。 专家站计算机装有RSView32组态软件、Matlab、VB、Access数据库等高级应用程序。专家站的主要功能如下: (1).管理整个控制系统,对系统突发错误作相关处理。 (2).对系统进行建模仿真及优化计算。 (3).根据专家经验给定投料量、焙烧窑转速等相关给定值以及各参数的报警上下限。 (4).建立各项指标数据库,将历史数据、操作报告、报警信息存入数据库。
3 OPC实现方法 3.1 组态软件OPC通信方法 现场操作级、工程师站和专家站计算机上都装有A-B公司的RSView32组态软件。该软件支持基于OPC技术的数据交换。将现场操作级的RSView32设定为服务器,工程师站和专家站的RSView32设定为客户机,现场数据及控制参数可以在三站之间双向传递。 服务器设定:假定煅烧车间1号工控机名称为Calciner1,在RSView32中建立一个新的节点: 数据源:OPC服务器 节点名:Calciner1 名字:RSI.RSView32OPCTagServer 类型:本机 更新速率:1秒 客户机设定:在工程师站和专家站上的RSView32中建立一个新的节点: 数据源:OPC服务器 节点名:Expert 名字:RSI.RSView32OPCTagServer 类型:远程 更新速率:5秒 需要注意的是客户机上OPC节点的更新速率应该小与服务器中OPC节点的更新速率。 客户机上RSView32中的标记需要连接到OPC服务器,将对应的数据名称设定为来自设备,节点名为Expert,地址填写为现场操作站RSView32中标记的名称。RSView32 的 OPC 服务器已经被测试和证明最多可以同时连接 10 台用作 OPC 客户的 RSView32 计算机,现在并不正式支持每台 RSView32 OPC 服务器与超过 10 台用作 OPC 客户的 RSView32 计算机连接使用。
3.2 组态软件与VB通信方法 专家站的组态软件通过OPC技术与VB连接起来,实现复杂控制算法。VB作为客户机与组态软件RSView32通信 方法如下[5]: 现在VB工具栏中“工程\引用”将Rockwell OPC Automation 2.0 加入。然后定义变量。 Const ServerName=“RSI.RSView32OPCTagServer” ‘ OPC类型 Dim Nodename as String ‘节点名即计算机名 Dim MyOPCServer as OPCServer ‘OPC服务器 Dim MyOPCGroup as OPCGroup ‘OPC组 Dim MyOPCItem as OPCItem ‘OPC项对象 Dim OPCItemCollection as OPCItems ‘OPC项集合 并定义项改变值个数、ID、指针等变量如: Dim ItemCount as Long ‘项改变值个数 Dim OPCItemIDs(100) as ‘定义OPC项数组 Dim ItemServerHandles()As long ‘定义服务器项指针 Dim ClientHardles(100)As long ‘定义客户端句柄 另外还要定义复杂控制算法中的全局变量如: Dim CalcinerHead_Temp as Single ‘定义窑头温度 Dim DischargeEnd_Temp as Single ‘定义出料温度 定义好所有的变量后,将进行OPC的连接,OPC读写等,由于程序较长,这里不再赘述。OPC客户连接后,需要占用服务器资源,所以程序结束后必须断开OPC连接,释放资源。关键程序如下: 清除指定的OPC项 0PCItemCollectlon.Remove ltemCount.Removelt emServerHandles,RemoveltemServerE1TOrS Set OPCItemCollection = Nothing 清除指定的OPC组 ConeetedServerGroup.Remove(”Group1”) Set ConnectedGroup = Nothing 与服务器断开连接并且清除 AnOPCServer.Disconnect Set AnOPCServer=Nothing 整个程序的流程如图5。
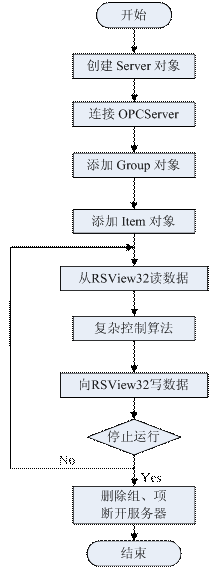
图5 VB程序流程图
4 结束语 根据碳素阳极生产过程的特性,借助PLC、RSView32组态软件以及VB等其他高级应用软件,采用OPC技术构建了现场操作级、工程师站、专家站三级控制网络。该网络结构具有以下优点: 1.现场操作站与PLC之间通过DH+ 网络进行数据传输,方便快捷,保证了系统的实时性。 2.工程师站与专家站采用OPC技术与现场操作站连接,这样减轻了DH+网络的通信负担,降低了因大量数据通信造成的控制系统的延迟。同时由于采用OPC技术通信后,工程师站及专家站工控机上无需DH+卡,减少了系统开支。 3.在专家站采用OPC技术将现场信息与VB、数据库等应用程序连接起来,增强的系统的可扩展性,其他控制系统开发商对控制系统进行优化升级时无需再进行重复的底层开发工作。
参考文献
[1] Jun Liu, Khiang Wee Lim. Using the OPC Standard for Real-Time Process Monitoring and Control [J].IEEE Software, 2005 22(6):55-59 [2] 李京,宋真君.OPC规范的产生与发展[J].自动化仪表,2002,23(4):68-70 [3] OPC Foundation. OPC Overview (1.0)[EB/OL].Http://www.opcfoundation.org, 1998-10 [4] 薛福珍,许磊,田贵宾,刘忍权.基于OPC的先进控制算法平台的设计与实现[J].自动化仪表,2005,26(9):26-28 [5] 赵艳秋,王建民.采用OPC技术实现竖炉烧结DCS系统与VB软件的接口[J].计算机与数字工程,2006,34:114-117
|